The dictionary of digital fabrication
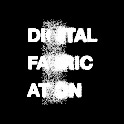
Additive methods In general, all those methods are additive methods that construct an object from a certain material. See →Contour crafting →Fused deposition modeling →Laminated object modeling →Laser metal forming →Selective laser melting →Selective laser sintering (SLS) →Stereolithography (SLA); for the opposite see →Milling and →Subtractive method.
Contour crafting (CC) Large components and even houses can be made by means of “contour crafting”. The process can be compared to →Fused deposition modeling – albeit on a different scale. Instead of using a →3D printer, here the individual layers are applied by a robot arm to which a nozzle is attached. The robot arm has the advantage of having a far greater working radius than a 3D printer. This process requires a fast-bonding material, for example concrete, to enable the layers to be added in swift succession. CC renders prefabricated components obsolete, as the object is manufactured in its entirety on site.
See →Additive methods
CNC mill CNC stands for “computerized numerical control”. A CNC mill is thus simply a computer-controlled lathe. On the basis of the data inputs, a milling head that can move across several axes is controlled such that by carefully removing material elaborate 3D objects can be made. “Milling centers” that operate across five axes are the most customary type of these machines. Today, there are even 12-axes milling centers that enable complex products to be manufactured in a single piece. For the opposite see →Additive methods
3D printer The label 3D printer is a catch-all for machines that can manufacture 3D objects on the basis of digital data.
see →Additive methods →Contour crafting →Fused deposition modeling →Laminated object modeling →Laser metal forming →Selective laser melting →Selective laser sintering (SLS) →Stereolithography (SLA)
Electron beam melting (EBM) EBM resembles Selective laser melting (see →SLM processes): metal powder and not plastics or other materials are melted in layers to create the desired item.
Fab Lab Is the abbreviation for “fabrication laboratory”. Fab Labs are workshops accessible to anyone using 3D printers, mills, computers, and other digital fabrication tools. The first Fab Lab was founded in 2002 by physicist and computer scientist Neil Gershenfeld at the Massachusetts Institute of Technology (MIT) in Boston. Gershenfeld’s objective is to open the new, digital fabrication methods and knowledge of these technologies up to the general public. Today there are more than 300 Fab Labs worldwide.
Milling Unlike additive methods, milling does not construct an object, but uses a rotating cutter to cut the desired shape out of the material. The workpiece is clamped into place and a milling head then cuts away the corresponding volume of material on the basis of digital data inputs. The method is frequently used in industrial manufacturing. Metals, plastics, wood, concrete, carton and many other materials can all be milled. See →Subtractive methods
Fused Deposition Modelling (DFM) Most 3D printers for household use operate on the basis of “fused deposition modeling”. Nozzles in the printer head heat a smeltable plastic and apply layer after layer of the thin, thread-like material until the preprogrammed shape literally arises. The printer head can move across the X, Y and Z axes. Depending on the number of nozzles in the printer head, different colors and materials can be included in one and the same process. The individual layers remain visible after printing. FDM has emerged as a comparatively cost-effective manufacturing process for small-sized items and prototypes. See →3D printer
Laminated object modeling (LOM) By means of “laminated object modeling”, wafer-thin layers are melted together – they can consist of aluminum, ceramic, plastic, or paper. The process is called “photo-laminating 3D printing” and is currently only suitable to make small or medium-sized objects.
Laser metal forming In the case of “laser metal forming” layers are melted to form the surface whereby almost any material can be used to this end. The material can either be in powder form, e.g., metal powder, or in the form of filler rods or wire. Heat is provided by a high-power laser (usually a diode or fiber laser) that melts the material applied. The method, as the name suggests, is only suitable for metal.
Rapid prototyping “Rapid prototyping” is the overarching label for mechanical manufacturing of prototype components and models on the basis of a digital dataset. The term thus covers all digital manufacturing processes. See →3D printer
Selective laser sintering (SLS) “Selective laser sintering” refers to a manufacturing process during which powdered plastic is heated under great pressure. The final product is, as it were, “baked” layer after layer. A large amount of powdered plastic (compared to the final product) is inserted on a coreboard on the Y axis. A digitally-controlled laser then sinters on the powder in line with the program. In order to harden another layer, the coreboard moves down a few millimeters and a blade creates a smooth surface so that the laser can harden the next layer. In this way, the object arises layer by layer from the powder base. The method can be used with materials such as plaster, ceramics, and metals. The components produced by SLS are relatively stable and precisely formed. SLS is preferred in various fields, for example to produce ceramic dental prostheses or components for the automotive industry. The process itself is not that unlike → stereolithography. See also: →Selective laser melting (SLM)
Selective laser melting (SLM) “Selective laser melting” involves melting layer after layer of plastic powder to bond them. The individual layers are melted in such a way that no air pockets arise, which spells a more solid and robust final product than can be achieved by →selective laser sintering.
Stereolithography (SLA) “Stereolithography” is an additive method in which the object is created layer by layer. To this end, a liquid, light-curing plastic is applied to a grid plate. A UV laser bonds and hardens the respective sections of the object in line with the data inputs. The grid plate is then lowered a few millimeters into a liquid plastic bath. The laser then hardens the next layer. This process is repeated until the object has achieved the desired shape, after which the item is hardened in a UV cabinet. The process is extremely precise and therefore suitable for medical and industrial applications. However, depending on the particular object’s size and complexity, fabrication can take hours or even days. See →Selective laser melting und →Selective laser sintering
Subtractive methods In general “subtractive methods” cover all those methods in which the desired shape is achieved not by adding materials but by removing material, for example by planning or milling. See →Milling; for the opposite see →Additive methods