Schöne, gedruckte Welt
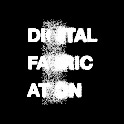
Unter den Auguren, deren Vertrauen in die Macht der Technik ungebrochen ist, hat sich in den letzten Jahren eine 3D-Druck-Euphorie ausgebreitet. Glaubt man ihnen, so wird so ein Gerät schon bald in jedem Haushalt stehen, was uns alle zu Designern und Produzenten werden lässt. Doch was ist wirklich dran am 3D-Druck für jedermann? Und welches Potenzial bietet er fürs Design?
Zunächst muss man wissen, dass mit dem Begriff „3D-Drucken“ Verfahren bezeichnet werden, durch die aus einem digital erstellten dreidimensionalen Modell ein reales Objekt in nur einem einzigen Schritt hergestellt werden kann. In Fachkreisen spricht man von „additiver Fertigung“ – in Abgrenzung zu subtraktiven wie Fräsen, Sägen, Bohren oder Wasserstrahlscheiden. Das bekannteste Verfahren ist die Schmelzschichtung, auch „Fused Deposition Modelling“, kurz FDM, genannt. Hierzu wird thermoplastischer Kunststoff wie Acrylnitril-Butadien-Styrol-Copolymerisat (ABS), Nyon oder Polylactid (PLA) in Form eines Plastikdrahtes durch eine Düse, die sich dreiachsig in die Höhe bewegen kann, Schicht für Schicht übereinandergelegt. Aber auch Ton, Metalle, Zement und sogar Lebensmittel wie Teig oder organische Materialien zur Herstellung von lebendem Gewebe lassen sich mit diesem Verfahren drucken.
Ein Ansatz, viele Verfahren
Während bei der Schmelzschichtung vorwiegend Kunststoffe verwendet werden, wird das Laser-Sintern sowohl für Kunststoff als auch für eine Vielzahl von Metallen wie Stahl, Titan oder Aluminium eingesetzt. Das neben der Schmelzschichtung zweitwichtigste Verfahren im Bereich der additiven Fertigung wird ebenso unter dem Stichwort „3D-Drucken“ geführt, gehört aber strenggenommen nicht dazu. Ausgangspunkt ist auch hier ein am Computer gestaltetes CAD-Modell, das mittels eines Lasers aus einem Pulver gewonnen wird, indem der Laserstrahl die für die Form relevanten Stellen verschmilzt. Eine Walze schiebt neue Pulverschicht nach, während die Bauplattform abgesenkt wird. Ähnlich funktioniert die Stereolithographie, mit dem Unterschied, dass hier das Pulverbett durch flüssiges Harz ersetzt wird. Eine dritte Fertigungsweise, bei der ebenfalls ein Pulverbett verwendet wird, ist das „Inkjet Powder Printing“, bei dem jedoch die einzelnen Schichten durch ein spezielles Bindemittel miteinander verklebt werden. Der Vorteil hierbei ist, dass so verschiedene Farben eingesetzt werden können – ebenso wie beim „Polyjet Printing“, das flüssige Photopolymere direkt auf eine Bauplattform aufträgt. Letzteres Verfahren geht aber noch einen Schritt weiter, indem man neben den Farben auch unterschiedliche Materialien während des Drucks miteinander kombinieren kann, etwa starre Kunststoffe mit weichem Gummi.
Veränderte Wertschöpfungskette
War es bislang der Industrie vorbehalten, komplexe Gegenstände zu produzieren, so kann das im Grunde genommen heute jeder, der einen 3D-Drucker besitzt (Preise ab rund 500 Euro, etwa von „MakerBot“) und sich entweder im Internet, in Open Source-Communities wie „Thingiverse“ oder „Shapeways“, einen Bauplan für ein 3D-Modell runterlädt oder ein digitales Modell in einem 3D-Modelling-Programm selber entwirft. Die Reaktion von Designern auf dieses Herstellungsverfahren fällt unterschiedlich aus. Der ehemalige BMW-Chefdesigner Chris Bangle schien vor wenigen Jahren fest davon überzeugt, dass in Zukunft jeder ein Designer sein werde und dass deswegen der Berufsstand unter Druck gerät. Designer wie Stefan Diez oder Sebastian Bergne sehen das gänzlich anders und glauben, dass dem Ottonormalverbraucher die Kompetenz fürs Design und die Bedienung der digitalen Werkzeuge fehle.
Tatsache ist, dass gegenwärtig vor allem kleine Gegenstände für den Hausgebrauch hergestellt werden können, wie Vasen, Handyhüllen, Zitronenpressen, Spielzeugfiguren und Modeschmuck. Eine zweifelhafte und fragwürdige Erscheinung ist der Druck von Waffen, wie es der amerikanische Student Cody Wilson mit seiner Pistole „Liberator“ vorgemacht hat. Etwas mehr Sinn machen da schon Ersatzteile für Geräte, die nicht mehr produziert werden und für die entsprechende 3D-Druckanleitungen im Netz zu finden sind. Seinen weitaus größeren Einsatz hat das 3D-Drucken schon seit längerem im Produkt- und Industriedesign um in kurzer Zeit Prototypen herzustellen. Aber auch in medizinischen Bereichen findet der 3D-Drucker vermehrt Anwendungsmöglichkeiten – beispielsweise für 3D-gedruckten Zahnersatz und Hüftgelenke. So lassen sich maßgefertigte Ersatzteile digital fabrizieren und herstellen.
Neue Druck-Ästhetik
Bereits 2006 entwickelte der französische Designer Patrick Jouin zusammen mit der belgischen Firma Materialise, die sich im großen Stil auf das 3D-Drucken spezialisiert hat und eine Kollektion 3D-gedruckter Objekte zum Kauf anbietet, den Hocker „One Shot“. Der Clou ist, dass der Hocker, der sich mit nur einem Griff zusammenfalten lässt, in einem Durchgang komplett mit Scharnieren und Gelenken gedruckt (in diesem Fall lasergesintert, mit Polyamid) werden kann – und auch tatsächlich dem Gewicht eines Menschen Stand hält. Patrick Jouin hat weitere Objekte entworfen wie die Leuchte „Bloom“ (ebenfalls mit Entfaltungstechnik) und den Stuhl „Solid“, der eine verzweigte Struktur aufweist, die nur schwer konventionell produziert werden könnte. So entstehen durch das 3D-Drucken Objekte mit komplexen Konstruktionen, die oft an biologische Strukturen erinnern oder aber die Ästhetik der 3D-Modelling-Programme, beispielsweise polygonalen Flächen, wiedergeben und auch ästhetisieren.
Eine weitere ästhetische Beigabe des Fused Deposition Modelling sind die geriffelten Oberflächen. Dirk Van der Kooji, Absolvent der Design Academy Eindhoven, hebt bei seinem „Endless Flow Open Rocking Chair“ den Aspekt des Schichtens deutlich hervor, indem die einzelnen Lagen, die durch den Druck entstehen, besonders groß sind und die Struktur des Stuhls prägen. Im Laden kostet Stuhl derzeit rund 800 Euro – nicht gerade etwas für den schmalen Geldbeutel. Bis heute ist aus diesem Prinzip eine ganze Kollektion aus Stühlen, Tischen und Kleiderbügeln geworden.
Während Van der Kooijs Maschine zum Stühle-Drucken eine Spezial- und Einzelanfertigung ist, bietet das Berliner Unternehmen mit „BigRep“ einen 3D-Schmelzschicht-Drucker für großformatige Objekte bis zu einem Volumen von 1,3 Kubikmeter zum Kauf an. Vor allem Designer, Architekten, Universitäten aber auch „Pro-Users“ seien an dem Riesen-Drucker interessiert, der mit 29.000 Euro zu Buche schlägt. Obendrein sei eine Kombination mit einer CNC-Fräse anstelle des Druckkopfes in Planung. Das wäre dann eine Art „eierlegende Wollmichsau“ unter Maschinen für die digitale Fabrikation, denn sie verbindet additive und subtraktive Verfahren. Und mit diesem Gerät wäre auch für kleine Büros und Unternehmen eine serielle Produktion möglich, die derzeit noch zu zeit- und kostenintensiv ist.
In Triebwerken und Karosserien
Vor allem die Großindustrie, die Luftfahrt- und Automobilindustrie, arbeiten schon seit gut zwei Jahrzehnten mit 3D-Druckverfahren und gelten als Innovationstreiber auf diesem Feld. Global operierende Konzerne wie Boeing und Siemens, aber auch die „Formel 1“ arbeitet mit Anlagenbauern wie EOS in München oder Stratasys mit Sitz in den USA und Israel, die zu den Weltmarktführern auf dem Gebiet des industriellen 3D-Drucks gehören, zusammen. Sie benötigen komplexe Einmalbauteile und drucken daher Verbindungselemente und Werkstücke mit Hohlräumen und filigranen Verstrebungen im Inneren, die in Triebwerken (Luftfahrt), in Karosserien (Motorsport) oder bei Robotern (Industrie) zum Einsatz kommen. Damit stellen sie günstige und schnell zu produzierende Alternativen zu herkömmlichen Verfahren wie dem Spritzguss dar. Und im Unterschied zum Produktdesign, bei dem der 3D-Druck vor allem fürs Prototyping nutzt, werden in der Luftfahrt und Automobilbranche die Stücke auch verwendet.
Um die additiven Fertigungsverfahren voranzutreiben kooperieren Firmen wie EOS, Stratasys und Siemens zusammen mit dem „Direct Manufacturing Center“ der Universität Paderborn (DMRC). Die Ingenieure arbeiten mit Hochdruck daran, dass in Zukunft die Geräte noch größer und schneller werden, beispielsweise durch den Einsatz von mehreren Lasern zur gleichen Zeit. Ihr Ziel ist es, mit dieser Technologie ebenso kostengünstig und schnell zu produzieren wie eine herkömmliche serielle Fertigung. Einen Schritt weiter gehen da Forschungsprojekte, die sich mit dem hybriden 3D-Drucken von Material und Elektronik befassen, um so dem gedruckten Objekt sogleich eine digitale Funktion einzuverleiben. Schwerpunkte liegen dabei laut Fraunhofer Institut auf dem Druck von Sensoren, OLEDs, Speicherelementen sowie von Batterien oder intelligenten Textilien. Anhand solcher Entwicklungen kann man sehr wohl nachvollziehen, weshalb das britische Wirtschaftsmagazin The Economist schreibt: „Der 3D-Druck wird die Welt verändern“ oder wieso US-Starökonom Jeremy Rifkin dadurch sogar eine neue industrielle Revolution erwartet.
Vom Produkt- zum Prozessgestalter?
Doch zurück zu unserem Ausgangspunkt: Welche Auswirkungen haben die digitalen Fabrikationsmethoden auf das Design? Wenn jeder alles produzieren kann, wo bleibt dann der Spezialist, der Schreiner, Designer, der Ingenieur? Man kann davon ausgehen, dass die Euphorie um den 3D-Drucker fürs Eigenheim abnimmt, nachdem man ein 3D-Selfie auf dem Küchensims stehen hat. Geht es nach dem belgischen Designerpaar Unfold, die sich selbst auf das dreidimensionale Keramikdruckverfahren spezialisiert haben, so wird der Berufsstand des Designers nicht verschwinden, er wird sich aber mehr auf Prozesse und Systeme als auf das Objekt konzentrieren. Und auch bei Siemens ist man sich bewusst: „Ingenieure müssen völlig umdenken“. Denn die Technologie ermöglicht einen „design-driven manufacturing process“, bei dem die Konstruktion die Fertigung bestimmt – und nicht umgekehrt, also dass die Grenzen der Fertigungsmethoden eben nicht schon die Konstruktion von vornherein beschränken, sondern Gestalter von Beginn an jegliche Freiheit haben, ihre Ideen zu verwirklichen. Für Gestalter und Industrie steckt also im „e-Manufacturing“ ein enormes Potenzial – als Treiber einer neuen digitalisierten Wirtschaftswelt, der „Industrie 4.0“, in der alles miteinander vernetzt ist und in der individuelle Wünsche, Flexibilität und Effektivität mehr denn je den wirtschaftlichen Erfolg eines Unternehmens oder Produktes definieren.