Data make clothes
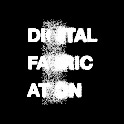
The concept of “digital fashion” is still in its infancy and the products it turns out may never really catch on. And yet, in light of recent trends such as jackets with integrated solar cells, lingerie with inbuilt GPS systems, and 3D-printed fashion items, all of which somehow fall under this definition, it should not be hastily dismissed.
In the last 150 years the pace of industrial production has quickened considerably, and in the process the clothing industry has spawned not a few trailblazing innovations. One such massive change occurred in the mid-19th century when craftsmanship became largely superfluous in mass production as a result of the introduction of mechanical and subsequently electric looms. Synthetic materials such as nylon and spandex, which debuted on the fashion scene in the 1930s, imbued textiles with new properties that made clothes comfortable and elastic. Ever since, there’s been no stopping advances to the synthetic fibers, which have likewise been tailored to specific applications. Take modern performance textiles, for example, which offer added heat protection or are completely waterproof thanks to nano-coating. Despite the ongoing optimization of clothing, one factor has remained constant in production, and that is that textiles are still being knitted or woven. Can digital manufacturing methods spell the end of this era?
Printed armor
For around four years now the eye-catching creations by Dutch designer Iris Van Herpen have been superb proof that fashion can indeed be printed. If, that is, we think of Van Herpen’s gowns not so much as items of clothing and more as art objects. Her output is more a matter of body armor for today’s amazons like Lady Gaga and Björk, both of whom Van Herpen counts among her clients. Her creations bring to mind the scales and shells of lizards, insects or aliens – and have a slightly morbid touch. Needless to say, this kind of fashion is hardly suitable for daily wear but is destined for mega-stage shows or displays on catwalks. Hardly surprisingly, Van Herpen presents her idiosyncratic creations at the prêt-à-porter shows in Paris, where the consortium of haute couturiers recently honored her with a young-talent award worth 25,000 euros.
The most striking thing about the phenomenon of Iris Van Herpen is how she goes about her work as a fashion designer: The fruit of joint computer sessions with architects, her styles are subsequently 3D-printed by Belgian specialist Materialise. Gone are the days in which patterns were cut, fabric pinned and sewed. For the coral-like skins of her “Voltage” collection last summer Van Herpen teamed up with Neri Oxman, founder and director of the “Mediated Matter” design research group at MIT. With Rem D. Koolhaas, nephew of architect and OMA founder Rem Koolhaas, she designs 3D-printed shoes for the former’s United Nude label – they are as audacious and unusual as her clothes. There is a pair, for example, that strongly resembles tree roots.
Iris Van Herpen is not the only designer to have her fashion “printed”: Since last year Burlesque dancer Dita Von Teese has been spotted wearing a breathtaking, 3D-printed dress – the joint brainchild of designer Michael Schmidt and architect Francis Bitonti. The black creation, which excessively accentuates the shoulders, consists of a flexible plastic mesh that was digitally precision-rendered to Dita Von Teese’s body and embellished with 12,000 Swarovski stones to intensify the extraterrestrial impression.
The creations of Noa Raviv, who was born in Tel Aviv and is now studying fashion design at Shenkar College of Design, are no less spectacular. Raviv likewise uses CAD programs in her work; however, she only prints the “skeletons” for her dresses, and then embroiders these patterns onto silk and tulle. The results are ephemeral patterns that reflect the formal aesthetic of CAD-rendered, organic shapes.
Kissing goodbye to lugging suitcases?
For the moment, Van Herpen’s and Raviv’s designs can be considered an extravagant albeit marginal phenomenon. And yet, digitally made fashion recently also made a splash on the mass market: In January 2014 the venerable fashion store “Pringle of Scotland” presented a collection of garments that had 3D-printed plastic parts stitched onto the fabrics. The printed plastic’s linked structure makes the “fabric” panels flexible, meaning that they adapt to the contours of the body, just like the textiles underneath. It was the birth of the world’s first 3D-printed prêt-à-porter range, or so the company proudly announced. The collection is currently on sale in stores and it will be interesting to see how the female clientele will respond to the high-tech fashion.
However, it is not only manufacturing methods that are adapting to a new era. Just as with other 3D-printed objects, in fashion too we like the idea of being able to compose our outfits according to personal tastes and produce them on demand. Finnish designer and 3D-printing pioneer Janne Kyttannen is showing us how exactly this might work. To alleviate the burden of travelers he has devised a “Lost Luggage Kit” that sends data files instead of a suitcase to the desired destination. These can then be used to print out clothes, shoes, bags and other holiday utensils locally as desired. Sounds like utopia? Then think again: There are plenty of items that are now part of everyday life which were initially dreamed up by authors of science fiction.
Lingerie that keeps tabs on you
Going one step further are smart textiles that respond to the environment, that glow and communicate, store energy or monitor the pace of life. It is hoped that such textiles will be increasingly employed in the healthcare and sports sectors, not to forget in architecture and in mobility systems. Networked high-tech fabrics are even being considered for everyday clothing as they communicate with the car or the environment or adapt automatically to changes in the weather. Consider the following examples: the sensor baby bodysuits by the Institute of Textile Technology and Process Engineering in Denkendorf (ITV), which monitors all vital functions. Or the lingerie by the Brazilian company Lindelucy, which has an inbuilt GPS transmitter. Even the German soccer team used smart textiles by Adidas when training for the 2014 World Cup – these transmitted information such as each player’s speed, the distance he’d covered, heart rate and performance to the coaches.
Textiles can also produce energy as Dutch designer Pauline von Dongen demonstrates – with her clothes that have solar cells embedded into them. We have all heard of watches and glass frames with Internet access, which would suggest that similar trends in the textile sector are only at the beginning. This is also evidenced by initiatives the world over, such as the “Computational Fashion” think tank in New York, which unites artists, designers and scientists and is supported by the “Rockefeller Foundation”. Then there’s the “Forschungskuratorium Textil”, the textiles research board founded by the German industrial association for textiles and fashion, the “Gesamtverband Textil + Mode“, which has set the development of technical and intelligent textiles as its top priority through 2025. Recently, the “Wear-It” festival in Berlin caused a real stir – it took place for the first time in early October 2014, having been organized by the makers and shakers and artists in the Trafo-Pop movement in Berlin, cyclists who rode around ringing their bells and wearing illuminated jackets. The guys and gals round Trafo-Pop founder Thomas Gnahm want to establish a network that tackles the issue of electrified, smart clothes from a playful, artistic perspective. Around 60 people, and not just Europeans, but also Asians and Americans, attended the two-day conference, which closed with a party at the Platoon with any number of smart art interventions (it attracted around 300). Maybe this way, the idea midwifed by the techy-users will also see the light of day among everyday users.
Seen in this light, “digital fashion” is the new avant-garde in the domain of fashion. The idea, of enriching clothes with new, digital functions let alone that of printing out cloths is without doubt fascinating. While smart textiles have long since been important in science and in the market, the future of printed fashion seems to rest on less solid foundations.
And yet, compared to these new material structures that tend to be made of plastic, it is traditional fabrics woven or knitted from wool, plant or synthetic fibers that have stood the test of time as tried-and-tested body exteriors for centuries: Not only are they comfortable to wear, warming and breathable, but they can also be easily altered if so desired. In this sense at present the idea of being able to print out clothes in the future seems as audacious as the Iris Van Herpen’s shoes. Let’s face it: Would you be prepared to swap a warm, cozy woolen coat for a cold plastic skin, or a flowing silk gown that flatters the human shape for one made of plastic mesh? Do you really think that United Nude’s polygonal plastic stilts will be able to outstrip a pair of welted leather shoes? Particularly so if we consider that the clothing industry as a global player is at present facing challenges of a very different nature: think working conditions as well as ethical issues as regards correct labelling and chemical treatment of fabrics. So the jury is still out on the question of whether future textiles will be knitted, woven or printed.
Further recommended reading:
Garments of Paradise
Wearable Discourse in the Digital Age
By Susan Elizabeth Ryan
MIT Press, June 2014, Cambridge
Hardcover, 336 pages
USD 35.00
www.textilforschung.de
www.fashion.eyebeam.org
www.irisvanherpen.com
www.francisbitonti.com
www.noaraviv.com