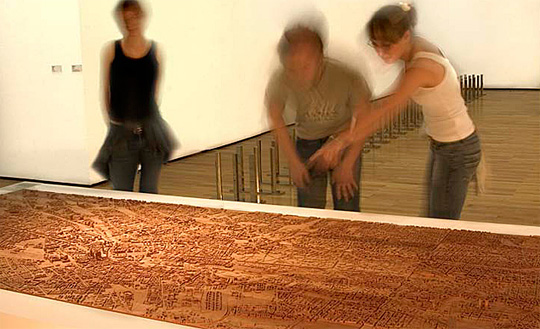
How can you convey an understanding of a city with a population of millions on a single square meter? Braunschweig-based firm scopulus, founded in 2005 by model builder Christian Werner and architect Dieter Hübner, has developed solutions to this problem. scopulus mills so-called GeoReliefs and CityReliefs for cities, communes, architects and landscape planners as well as tourism associations, companies and private clients. The origin of scopulus can be traced back to classic architectural model construction. In 2000 an architect asked Christian Werner for a "hand luggage-size city". He needed a handy city model for a presentation for an international urban planning competition for Luchao City, China. The answer was a model on a scale of 1:20,000 on a compact 64 x 64 Centimetre base, milled from a solid wood for the first time. The development of the milling technique had already begun a few years before, flowing from the demands of high-level model construction. Now their task was to obtain the relevant data but parallel to the design process, and to put the data in a three-dimensional structure and on a suitable scale. This transferal process has not changed to this day. The amount of time it takes (the calculations alone can take several days) gives an idea of the complexity of this process. In the meantime, measuring the world has also advanced at an unimagined speed and has made ever more new and better data accessible to the public. From the very beginning, at scopulus the intention was to try and be a counterweight to the abstract, over-technical and highly complex process of data modulation by instead deploying especially familiar, original and yet equally timeless materials. Thus it is no wonder that they prefer to use wood, a 70 year old tree provides a particularly worthy material for 1000 hours of work. They use and combine types of wood which woodturners also like using, such as, for example, the reddish brown high-quality wood of the wild service tree (Swiss pear tree), one of the hardest European woods, which once dried, holds its shape especially well. Naturally, parallel to this scopulus also works with classic model construction materials, block materials and with acrylic glass, as well as aluminum alloys and soft stones such as marble and alabaster. Which tools are selected depends on the requirements of the material. At present, a computer-controlled milling cutter produces the most precise results while simultaneously being able to process a wide variety of materials. The complexity of programming and processing time for a city model amounts to almost 1:1. Mistakes are to be avoided at all costs, because in milling there is no "undo" button and errors would show directly and permanently in the shape. Milling times for a one square meter and highly detailed city model amount to 300 to 500 hours. The time depends directly upon the smallest tool used. For the finishing touches, scopulus uses a milling cutter with a diameter of 0.5 mm or less. Depending on the material, after milling the reliefs are worked up by hand. The wood reliefs require an especially long time. They must be carefully "cleaned" to remove protruding wood fibers and burrs, which can take up to an additional 100 to 150 hours. The final surface treatment is also specific, for example, linseed oil is a favorite for use on wood. These finishing touches by hand refine the milled form and require a great deal of skill and concentration. Without doubt, the fascination of the models consists in their games with closeness and distance, depth of sharpness and texture. The objects only look smooth from a distance; on closer inspection every surface becomes a relief, an exciting topography in which expansive landscapes or cities are depicted in miniature and at the same time tiny inconspicuous things are made tangible. At scopulus, high-tech, mechanical processing and skilled work by hand combine to form a modern production facility, sculpture with different means, so to speak. A few small series aside, most of the objects produced thus far are single pieces. However, projects involving larger numbers using milling technology and casting processes are in development. For scopulus, the huge amount of work involved coupled with the associated latent economic inefficiency is the best protection against copies and guarantee of the uniqueness of each and every model. Even with the best photographs, relief surfaces cannot be reproduced without losing some of their sensory appeal. Thus for those who are interested, a visit to scopulus in Braunschweig is highly recommended.
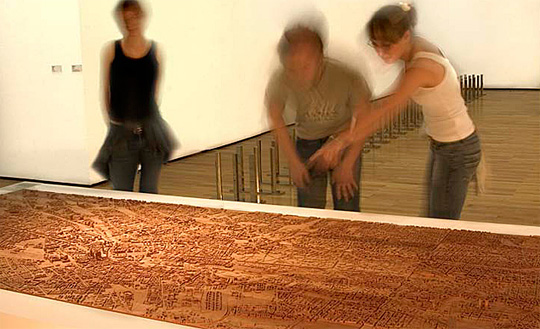
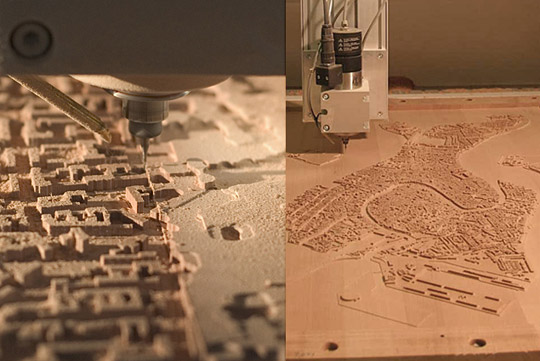
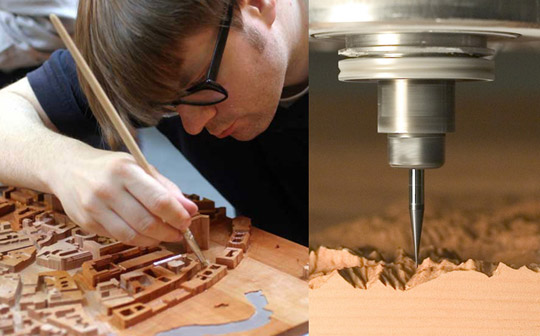
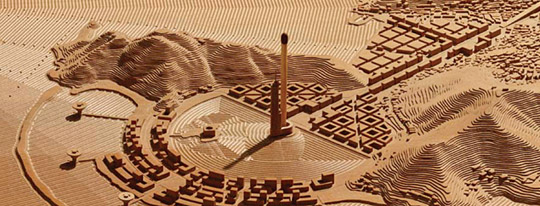