Weave replaces brickwork
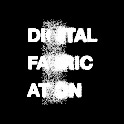
The wish to be able not only to design, but also to build free, organic forms is far older than the options the digital age offers us. This is evident even if we restrict ourselves to the recent past: In the first half of the 20th century, Le Corbusier believed in freeforming concrete and using it for structures with incredible spans. Oscar Niemeyer’s concept of architecture was inspired by the forms of the female body, and since the 1950s, the name Frei Otto has stood for tent-like roof structures with no intervening supports. Frei Otto was also the person who laid the foundations at the University of Stuttgart for a culture of engineering research as part of architectural studies. Research was conducted into what is intrinsic to digital fabrication, namely the properties of the respective construction material.
Understanding the behavior and properties of the material
Once fabrication methods and machines are employed that have nothing to do with masonry and bricks, the behavior of the materials becomes a decisive parameter. That also goes for weave buildings. The weaving of buildings is the main field Achim Menges is currently researching. He is an architect at the Institute for Computational Design ICD at the University of Stuttgart and collaborates with the university’s Institute of Building Structures and Structural Design (ITKE) to develop experimental buildings that reflect the current research status of design and manufacturing techniques in architecture. The very latest “ICD/ITKE Research Pavilion 2013-14” opened in March 2014, was made by robotically weaving glass and carbon fibers soaked in epoxy resin. Two industrial robots capable of moving along six different axes weave these fibers around a total of 36 thin frames, which define the edges of the components and were removed once the individual modules had been woven.
Learning from the wing shells of flying beetles
Two areas of research were conducted within the project: robotic production methods for fibrous composites and the biological construction principles of natural fiber structures. The shells encasing the wings of flying beetles inspired the structural principles underlying the bionic pavilion. Such wing shells not only protect the beetle’s abdomen, but are also low in material and weight to preserve the beetle’s ability to fly.
Once the properties of these shells had been recorded using a micro-CAT scan it was possible to draw conclusions about how the weaving syntax was to be executed. Combining these results with the interaction between material, form and robotic manufacture produced innovative lightweight construction methods using fiber composites.
Textile materials offer the most options when it comes to free-form structures. However, their use is limited by their not having load-bearing properties, and consequently the construction process largely revolves around developing a basic structure that is sturdy and can be formed.
Construction process as form generator
With regard to computer-based architecture Achim Menges also calls for people to revise their ideas regarding architecture’s material qualities: “Where machine and material not only overlap in the design process, but also interact this creates a new concept of material in architecture.” Accordingly, the predefined behavior of the material along with the basic structure decide the pavilion’s design. It is the building process that engenders the final shapes.
This example demonstrates that digital fabrication makes architects reconsider the use of certain materials and fundamentally alter their relationship to them. A new culture of materials emerges as a result. The question is then not so much what a material “looks like”, but how it behaves and how malleable it is. Architects might have long believed that such questions had been answered in principle, but they are now facing them anew. Especially as people wish to abandon or at least move away from the construction methods already used 2,000 years ago. And another thing is likewise clear: Digital fabrication does not start in the factory where data is transmitted to machines and the desired components are produced. Robotic weaving methods demonstrate that computer-based design and development are already part of the construction process.