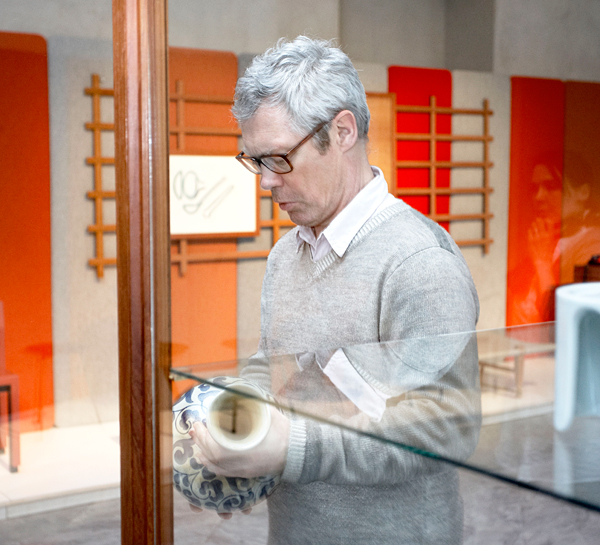
“Everything is running smoothly. And you?” reads one of the status reports issued by the computer “HAL 9000”, the most perfect machine of all times, to astronaut Dave. We know: Everything is running anything but smoothly. “HAL”, the famous computer in Stanley Kubrick’s “2001. A Space Odyssey” is a relentless machine that refuses to be switched off. Quite the opposite of Jasper Morrison’s “HAL”, of which, following the launch of models for the office at Orgatec 2010, Vitra is now showcasing new versions for the house and home in Milan. It is unspectacular, the sort of thing that needs a second look. And first and foremost to be tried out. For it has all it takes to become a genuine all-rounder. Thomas Edelmann met Jasper Morrison to talk about this and other things. Thomas Edelmann: You grew up in New York. Today you live and work in Paris, London and Tokyo. What role do these cities play in your work? Jasper Morrison: All these places shape and influence me. Even if it were five or ten different work locations, it would not bother me. And I would definitely also include Milan and Basle. I am interested in different lifestyles, the atmosphere, but things from the past as well, I find all that very inspiring. I got a lot of energy from opening up a studio in Paris. How many people in total work in your studios? Morrison: Not many. We are seven in total. We would easily fit into just one room. We have ten workstations in London alone, and they are never all occupied. But if we were all together in the one room, productivity would most likely suffer as a result, I myself would certainly be less productive. In Paris we mainly make chairs and other furniture, in London the other products, while in Tokyo the focus is on Muji. It’s very nice to arrive at a new place with fresh ideas and then work on a project. The “HAL” chair looks very simple. How is a concept design transformed into the final product? Morrison: In Paris I work on a range of chair projects together with Jun Yasumoto. We are experienced in this particular area. I draw while he assembles the pieces on the computer until something transpires that makes sense. In the case of “HAL” we sent the results to Vitra, after which we made models and prototypes. This went back and forth more than 15 times. At the beginning of the project the individual steps were really large, towards the end they became much smaller. The engineers from Vitra, Rolf Fehlbaum and Eckart Maise, provided a lot of input, for example, where their ideas of comfort and appearance are concerned. We got immersed in many in-depth discussions. This is anyway a trend that is becoming ever more important: design as a product of shared discussion. The process no longer involves so much drawing or contemplating ideas on your own in the studio but is a development that evolves in the course of various project meetings. For me that is the key – a good project is extremely productive in this regard. What is the starting point of a project like this? Morrison: It’s different each time. You just can’t predict how things will kick off, and what shape they will take. In this case everything revolved around the shell, the common element that links all the different models of the chair, while the base provides variety and makes “HAL” into an all-rounder. There are models with runners, with four single wooden legs, even a cantilever chair, and each of them looks very different. So the connection between the shell and the base is the crucial element in “HAL”? Morrison: Yes. It was really difficult and gave us quite a few headaches. Because each base, no matter how different it is, has exactly four connection points with the shell, and they have to match precisely on each model. It meant a lot of work; drawing, redrawing and redrawing yet again. When the chair was launched at Orgatec last year, we were still busy working on the second product wave that is now being showcased in Milan. What is the basic idea? Morrison: The shell is neutral enough to harmonize with a wide range of different situations and environments, while at all times maintaining a clear identity. The major investment for the company was the shell, not the base. Which is why a lot of care went into the developing process. It is probably the first shell seat that can be fully shredded and recycled. The shell contains no metal components. For the four bolt connections we integrated a nylon insert in the shell. A neat solution. Steps such as these, however small they may be, are important in that they set a new standard. It’s good to incorporate the advantages cutting-edge technology offers in a new project. What defines a good chair? Morrison: If it is a shell chair such as “HAL” it’s important that the backrest does not lean too far back when you sit down. That said, it should still give a little as well. It was important for us for the chair to provide a wide range of different positions, i.e., so that you can sit sideways or astride without the shell getting in the way. And there is no easy solution to that. Another challenge was to attach the legs or runners such that the shell and base together always create an attractive overall appearance. What was even more difficult was designing stackable models. The shell is reinforced on the side, what is the idea behind this? Morrison: You only ever use material where it is required. It’s a question of load-bearing structure and saving material. You are one of those designers who have not specialized in any particular field. You design furniture, but your previous work also includes a streetcar, household appliances, refrigerators and telephones, to name but a few. Are these tasks essentially very different, designing furniture on the one hand, and the more technical objects on the other? Morrison: For me, working on a range of highly diverse projects all at the same is a positive thing. The work process always involves several steps. And if, two weeks down the road, you return to an extremely complicated project for which there previously seemed to be no solution, the problem suddenly evaporates. It would be different if you only busied yourself with chairs or mobile phones. Variety keeps me interested. Often there are cross-references, small discoveries you make during one project that enrich your work as you can apply them in a different context. Why is it so difficult to improve the design of electronic equipment? Morrison: I worked for Samsung for several years, during which time some really good projects came about. One of the major problems is that often the companies are too large to get any “sense” in the project. The meetings are sometimes attended by people who are simply not used to moving joint projects forward. Those involved lack a common denominator motivating them. It may sound silly, but often no one in the company is prepared to assume responsibility for a project, to stop things if they move in the wrong direction and crucially steer things back on track. And that is precisely what Rolf Fehlbaum at Vitra does repeatedly. And there are no comparable structures in place at manufacturers of electronic goods? Morrison: The problem is often their strong market position, their large quantities mindset. That prevents consistently pursuing new paths. We recently designed a cordless telephone. The company, “Punkt.”, is new. A very small firm, where we were able to gather round the table and discuss each particular aspect. My job was to strengthen the position of the design. We also defined the agenda for the new company. What distinguishes the new telephone from existing designs is that it keeps to the basics while boasting some improved features for everyday use. In Milan we are presenting a new alarm clock based on the same principles. In the course of your career you have designed numerous chairs and in 2009 you curated an exhibition on chairs in Paris. Why can designers never stop thinking about chairs? Morrison: Because there is always room for improvement. Occasionally, not always, you can improve their ergonomic design, their comfort, they way in which they are assembled, or cut production costs, which has a positive effect on the price. It’s an evolutionary process, and chairs in general are improving on the back of it. They are getting lighter, easier to produce and can be better recycled. Anywhere there is room for improvement it is happening. Generally speaking it is a good thing for lots of people to be interested in designing and producing new chairs. Because by no means all of them go into mass-production, this is not a problem and only rarely does a bad chair have any success in the market. What role do your earlier chairs play for you now? Morrison: It’s like a family tree. You should not be too embarrassed about your old projects. They represent me at a particular time. The better ones led to further projects, some of which I am still involved with today. Last year in Kortrijk I only showed designs I created between 1981 and 1989. I tried to reconstruct the context of the time with drawings, magazine articles and other written material. It was a peculiar feeling, show all these old things without including anything new. You run a store – online and as an actual store – in London. There you sell your own products as well as items you developed together with Naoto Fukasawa in the context of your “Super Normal” project. What does this project mean to you? Morrison: It is something in between store, showroom, and museum. We have three kinds of customers. There are those who just look around and don’t even buy a postcard. Others come with the intention to buy. And then there are those who want to see my products and find out what’s new. During London Design Week we have always had a themed exhibition in the back room. Last time it was about trays from the world over – while in the room facing out onto the road we launched three new products, including the telephone we spoke about earlier, a shoe for Camper, and a wristwatch for Rado. It is not a commercial but a cultural project because each time we sell something we actually lose money on it. The store pays no rent and has no employees. When the doorbell rings, someone from our London team, all well-paid designers, will go into the salesroom and stay for as long as someone is having a look around. The store is an important project for us because it closes the circle. We deal with manufacturers and with retailers, but seldom do we get to meet the people who buy our products. It is a way of communicating, we are part of the city. It was Sori Yagani in Japan who introduced me to the concept of the combined studio and store. I thought that was an excellent idea. How has design changed? Morrison: It has become attractive to a larger group of people. More people are interested in it, though some of them possibly for the wrong reasons. Often it is more about the performance of the marketing strategy and not so much about the consumer. For me that is the negative side to design. That said, nowadays we are far more involved in the industrial process than we were in the 1980s. Today we exchange three-dimensional construction data with the companies, in the past we had to send copies of our drawings to the respective firms and for the prototype would receive at best an interpretation of our ideas. Studios need to get serious about immersing themselves in product development. Like Dieter Rams did it in his day, more than most of us nowadays. But perhaps it’s just me who has grown old – or just more mature. Current exhibition:
Danish Design – I like it! Jasper Morrison
From April 8, 2011 through January 2, 2012
Designmuseum Danmark, Copenhagen
http://designmuseum.dk
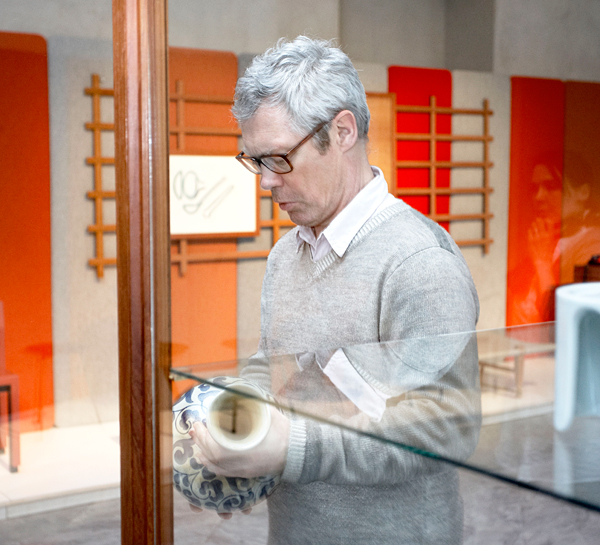
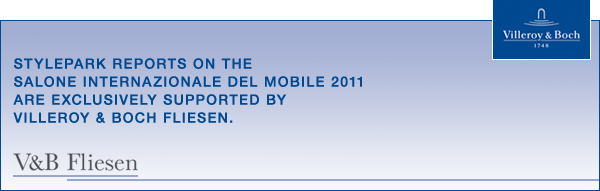
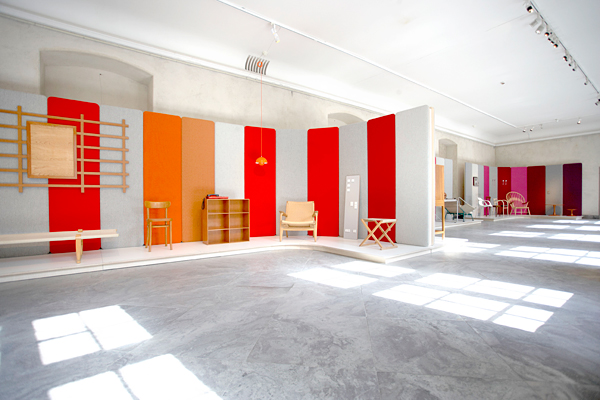
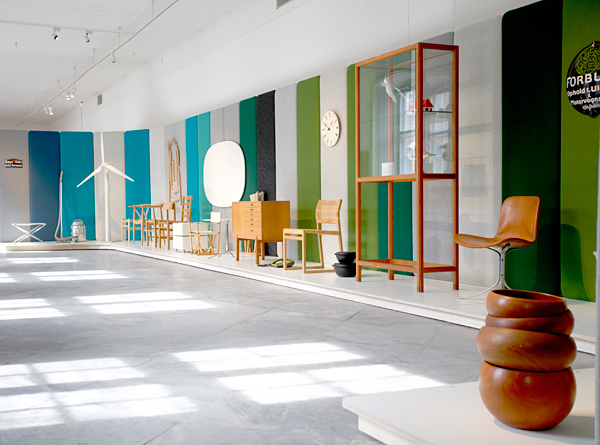
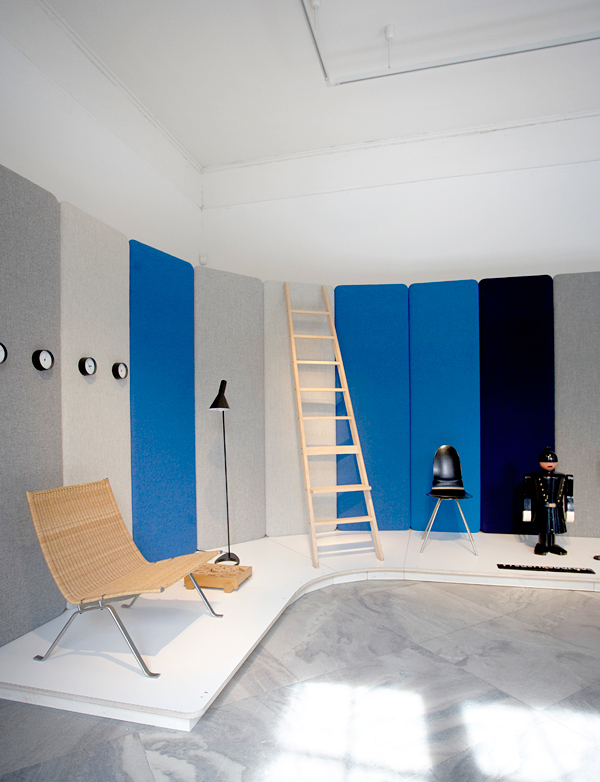
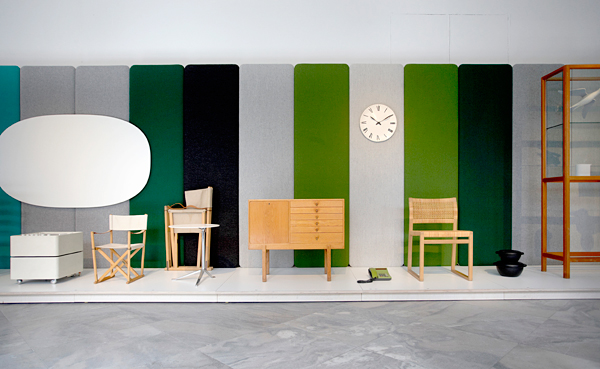
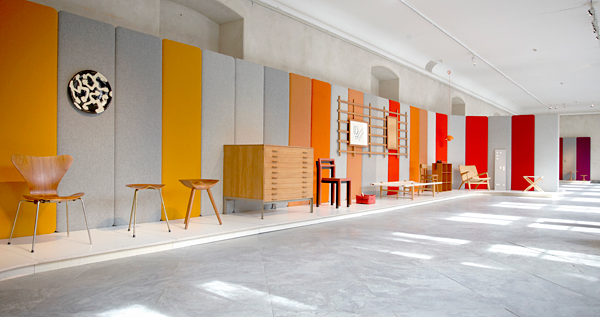
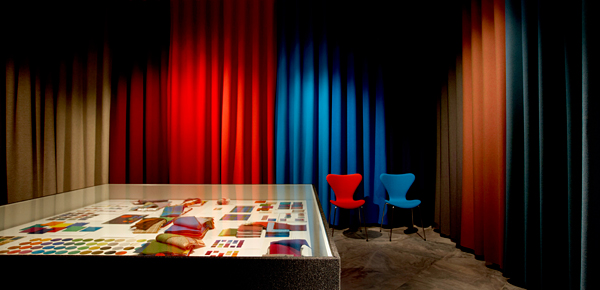
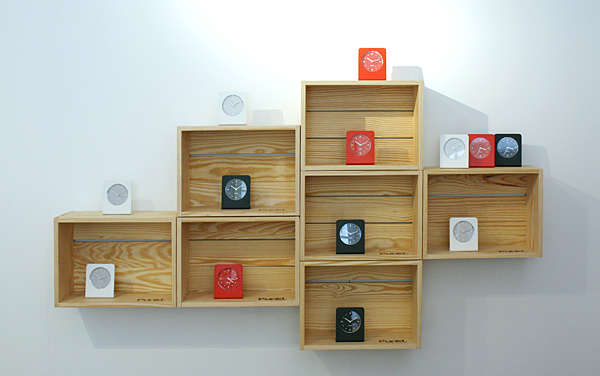
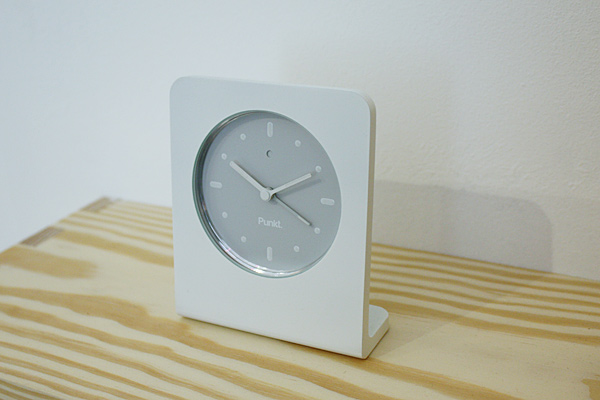