Printing construction
It is a bit like the race for space: Wherever you look worldwide, architecture projects are currently being promoted with titles such as “The world’s first commercial housing project based on 3D-concrete printing”(Eindhoven) or “The first German home straight from a 3D-printer” (Beckum). 3D-printing and the digitization of the construction sector that goes along with it really seem to be taking off – and everyone wants to contribute their own superlatives. High time, or so you might think. After all, the building industry cannot exactly be described as embracing innovations despite having an immense number of products, which is why we persist today thousands of years down the line in layering bricks one over the other. More recently it was glass and concrete that as materials in the modern age were intended to bring light, air and creative scope into architecture in the 20th century. Meanwhile we have arrived in the 21st century and now it is 3D-printing that could provide the prospect of a new approach to construction.
So what exactly makes 3D-printing so innovative? If you look at the two examples mentioned at the beginning – the residential buildings in Beckum and Eindhoven – it would not necessarily appear to be the case that the creative potential of the new technology has produced pioneering architectural achievements. Admittedly, they do boast a wealth of curving forms that are presumably intended to illustrate that the method can really deliver on expressiveness. That said, it is easy to think of countless architects who did a much better job using concrete decades ago, Brazilian Oscar Niemeyer and the recently deceased Gottfried Böhm being but two outstanding examples. In other words, it must be the process of construction itself that is so intrinsically revolutionary. And indeed, one advantage concrete 3D-printing has over conventional construction with concrete is that formwork is no longer needed. Instead, the house is built by a 3D-printer placed on the construction field which applies a special concrete layer for layer to make the individual components and even makes allowances for the recesses and niches that will take the technological fittings. However, it is not possible to forgo human assistance altogether – for instance, the lintels have to be mounted by hand.
The process saves time, construction workers, and material; this brings us into the realm of inexpensive building which incidentally was also a promise associated with "old concrete" back in the 20th century. It is therefore hardly surprising that industry has embraced the subject. One such example is the company ICON that is financed by a group of investors including Danish architectural firm BIG. The portfolio of the American company includes two roughly 46-square-meter large houses in Tabasco, Mexico, erected as part of a pilot project to create affordable housing. In Russia and China, 3D-printing is also very much in evidence: In 2017, Moscow start-up "Apis Cor" produced a 38 square meter house in the space of just 24 hours while back in 2014 the Chinese firm "Winsun" assembled ten houses from individual 3D-printed wall elements in the same time. The construction material was a mixture of fiberglass, cement, and recycled building rubble – whereby this last ingredient meant a small contribution had been made to a favorable ecological footprint. Notwithstanding this, printing with concrete is anything but sustainable as concrete remains concrete regardless of whether it comes out of a printer or formwork.
A recently completed pedestrian bridge in Amsterdam demonstrates how complicated holistic sustainability is when it comes to the construction sector. Designed by Joris Laarman and realized by Dutch robotics firm MX3D "the first 3D-printed bridge of stainless steel" was made in a factory by six-axis robot arms fitted with welding devices and fabricating 4,500 kilograms of stainless steel over a period of six months before then being assembled on site. According to MX3D's co-founder Gijs van der Velden thanks to the use of robot technology the project structure is optimal. However, once again despite being long lasting and recyclable the material used is not sustainable since a great deal of energy is required in its manufacture. So what material would make ecological sense for 3D-printing? Italian firm WASP relies on clay. And it has already used it to make several huts including a 60 square-meter tiny house designed by Mario Cucinella Architects with a kitchen and bathroom. The material used for it was excavated not far from the building site and subsequently layered to create two dome-shaped volumes with the result that the architecture is not only more sustainable, but also looks it.
It would seem that despite the many options available, architects remain hesitant to employ the new technology. That said, initial scenarios have been outlined that go beyond experimentation with shapes. For example, Dutch architecture practice OMA addressed the use of 3D-printing in its "The Hospital of the Future" project in order to design more flexible typologies for hospital construction. And as regards sustainability there have been a number of approaches that do not necessarily need to end in clay huts: Munich start-up 3F Studio produces a facade element called "Fluid Morphology" that comes straight out of the 3D-printer. It is made partly from old PET bottles and as such doubles as both insulated protection from the elements and sun but also as an acoustic panel. A similar approach is pursued by the "Smart Slab" project that was developed in the Chair for Digital Building Technologies at ETH Zürich. It is the "first load-bearing concrete ceiling slab produced using 3D-printed formwork". The result is a delicate ceiling with decorative structures on the underneath that is not only 70 percent lighter than a conventional concrete ceiling but also requires a good 60 percent less material.
In other words, the options afforded by 3D-printing could result in a new architectural vocabulary that ought to be of interest in particular to the grand expressionists among the architects. It therefore comes as no surprise that Zaha Hadid Architects have just completed a bridge made of unreinforced concrete developed in collaboration with the Block Research Group (BRG) at ETH Zürich. The structure realized for this year’s Architecture Biennale is composed of hollow, wedge-shaped 3D-printed blocks that are simply held together by gravity. They form a kind of arch that distributes the weight to the foundations and takes its cue from the load-bearing principles of Gothic cathedrals. Incidentally, and this is only mentioned for the sake of completeness, the bridge is the "first 3D-printed bridge of its kind".
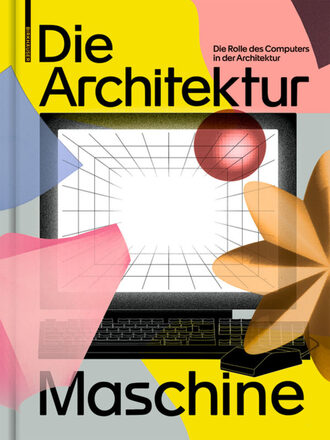
Book tip
Title: Die Architekturmaschine – Die Rolle des Computers in der Architektur. (The Architecture Machine - The Role of the Computer in Architecture.)
ISBN: 3035621551
247 pages
Language: German
Edited by Teresa Fankhänel, Andres Lepik
Birkhäuser Publishing House
39,95 Euro